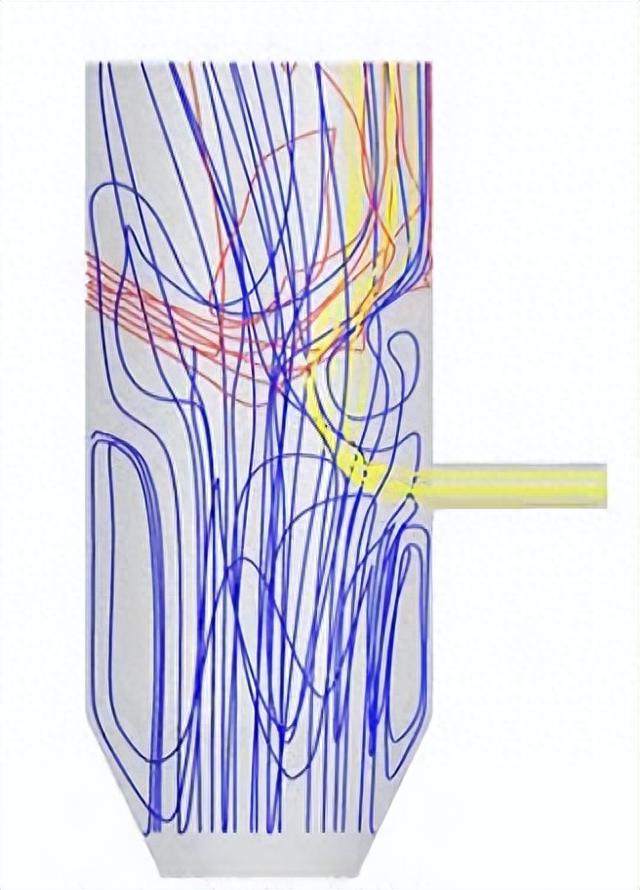
文:奇闻馆长A
编辑:奇闻馆长A
●—≺ 前言 ≻—●
磷石膏是磷酸制取过程中产生的主要排放物,其主要成分是二水硫酸钙(CaSO4·2H2O),含量达到90%以上,是一种重要的石膏资源。
由于磷石膏中含有少量的游离磷酸及其盐、有机物等多种杂质,在回转式反应器内进行硫磺分解磷石膏过程试验,其反应停留时间长达60min、硫磺间接换热效率低,难以实现工业化过程。

利用硫磺窑外还原分解硫酸钙的新工艺,即在窑外悬浮还原炉内进行硫磺还原硫酸钙的部分还原,在窑内继续进行硫化钙的氧化分解。
能够大幅增加系统反应效率,使煅烧窑炉内的物料停留时间减少30min,同质还原能够增加系统内SO2纯度的同时有效降低窑炉碳排放,降低生产成本的同时提高了生产力。

本文结合硫磺窑外还原磷石膏新工艺关键设备及实际试验工况,基于Fluent软件建立1:1还原炉模型,在欧拉-拉格朗日体系基础上,多相流采用组分运输模型。
化学反应采用有限速率/涡耗散模型模拟系统还原炉内生料分解的多相反应过程,为该系统中还原炉的系统优化提供理论基础。
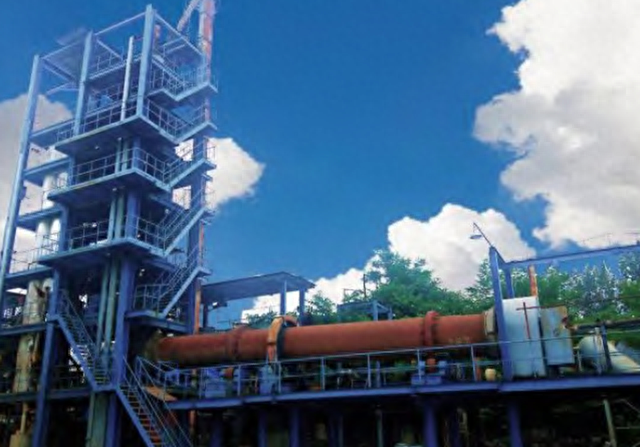
●—≺物理模型≻—●
根据气体硫磺还原磷石膏系统还原炉的内部结构建立几何模型以及网格划分,还原炉为外循环式高固气比还原炉,窑尾烟气从还原炉底部缩口进入,生料入口和气体硫磺入口分别位于还原炉主体下段两侧。
由于计算流场是有多相流化学反应的复杂流场,网格质量直接决定计算收敛速度和模拟精度,故选用Fluent-Meshing对上述几何模型整体划分为四面体-六面体混合网格,对各个入口进行局部网格加密,以便更好的捕捉计算结果。
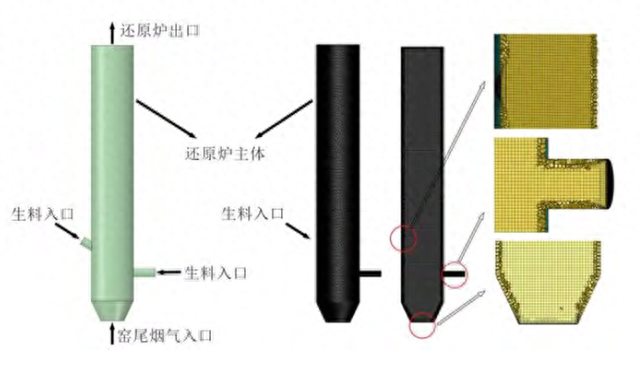
●—≺数学模型和数值方法≻—●
由于计算流体动力学方法日益成熟,数值模拟已广泛应用于预还原炉的设计和优化。
欧拉多相流模型能够很好的描述多个独立但又相互作用的相,与欧拉多相流不同的是,组分运输模型更能模拟混合物各组分之间或与其他相之间的相互作用,故对于还原炉内的多相混合状态的模拟选择组分运输模型更为合适。
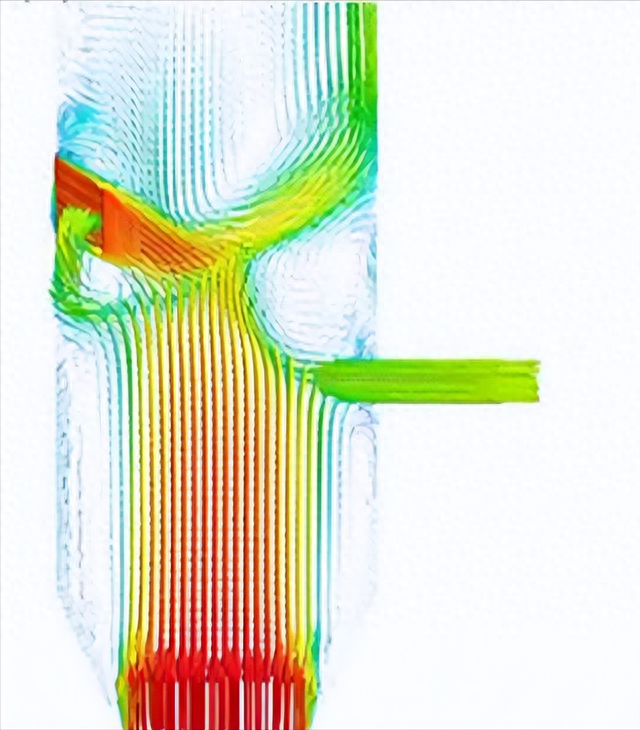
计算流体力学遵循三大基本物理定律,即质量守恒、能量守恒、动量守恒。
对于包含有化学反应或不同成分混合的湍流流动,系统还需遵循组分守恒和湍流运输方程,控制方程即是通过数学公式描述守恒定律,各守恒定律相对应的控制方程。

对于不可压缩稳态流体,密度(ρ)为常数且不随时间变化,上式可简化。
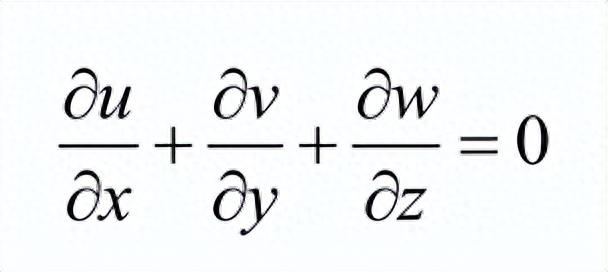
动量守恒方程。
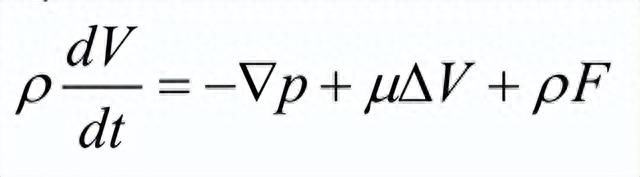
能量守恒方程。
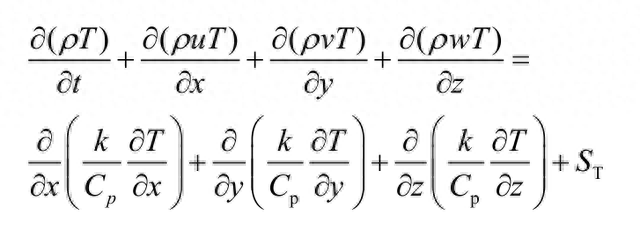
多组分反应流体守恒方程,即每种组分遵守组分质量守恒定律。
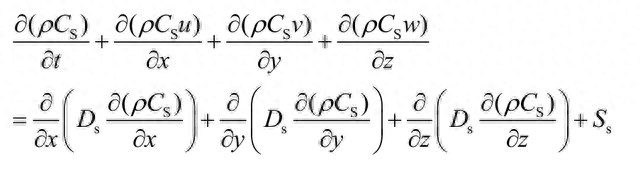
采用带旋流修正的k-ε双方程模型作为湍流气相流动模型。
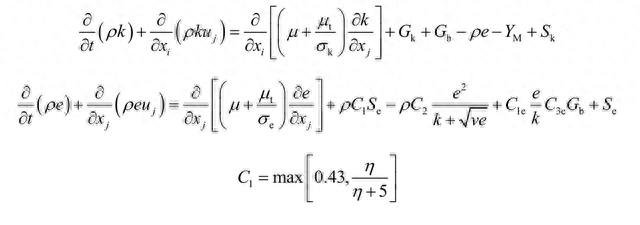
该模型选择在连续相的欧拉坐标系下,采用拉格朗日方法追踪颗粒的运动轨迹,也称为离散相模型。
由于炉内流动是强湍流流动,湍流脉动对于颗粒群轨道的影响采用随机轨道模型计算,考虑重力和曳力作用,忽略其他作用力的影响,颗粒在笛卡尔坐标系下的作用力平衡方程。
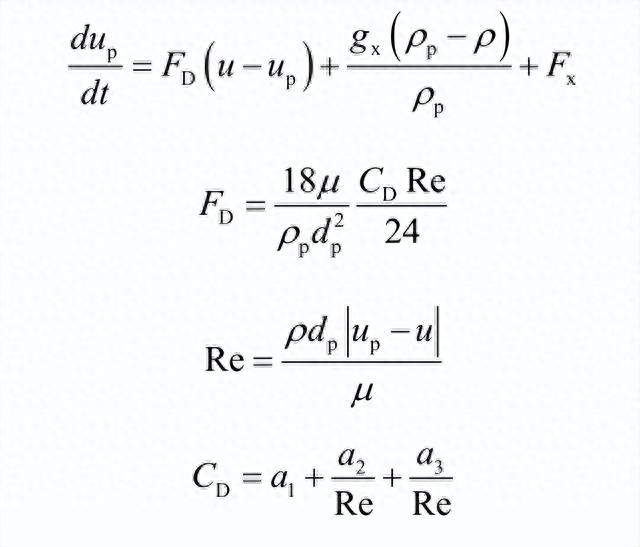
炉内涉及生料颗粒在气体硫磺还原下的化学反应,故选取湍流化学反应模型为通用有限速率模型,即通过求解化学物质的组分守恒方程预估每种物质的质量分数,守恒方程的通用形式。

系统中若有N种物质,需要解N-1个方程,N种物质的质量分数总和为1,第N种物质的质量分数通过相减所得,所以第N种物质须为质量分数最大的,以使数值误差最小。
化学反应与湍流的相互作用采用涡耗散概念模型,涡耗散概念模型是涡耗散模型的扩展,涡耗散模型由湍流主要控制化学反应速率,避开了复杂的阿伦尼乌斯化学动力学计算,而涡耗散概念模型使细致的阿伦尼乌斯化学动力学在湍流中合并。
涡耗散概念以在湍流流动中包括详细的化学反应机理,它假定反应发生在小的湍流结构中,成为良好尺度,良好尺度的容积比率按下式模拟,认为物质在好的结构中,经过一个时间尺度τ*后开始反应。

缩核模型用于描述多孔颗粒吸附气体的化学反应,该气固反应模型所涉及的微观物理化学步骤与其他模型类似。
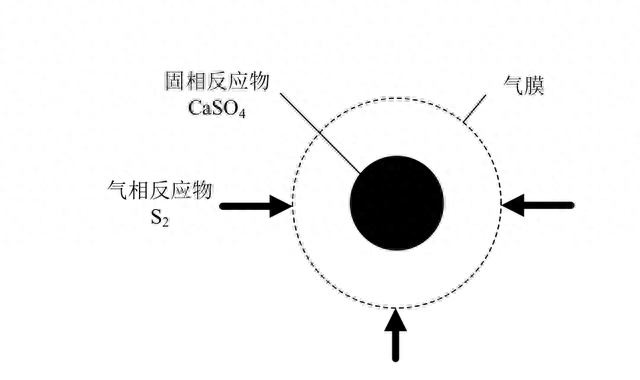
气相分子从气相主体向固相颗粒外表面扩散,外扩散过程,固相颗粒表面的气相分子进一步通过颗粒孔隙进行扩散,内扩散过程。
气相分子在局部固相颗粒表面发生化学反应,表面反应过程,反应物分子通过产物层扩散后进一步反应,固体产物逐渐生长导致固相颗粒结构变化。
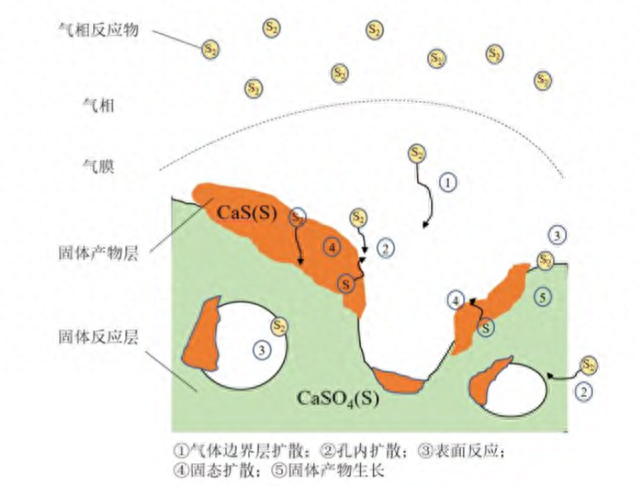
还原炉中气体硫磺与硫酸钙的反应属于气固非催化非均相反应,其反应模型基于气固反应缩核模型,固相反应物核外包裹一层气膜,气体硫磺穿过气膜与硫酸钙反应。

在该模型中假设气体硫磺还原硫酸钙颗粒过程中固相颗粒直径不变,而颗粒密度减小,其反应速率表达式。

碳酸钙粉状细颗粒在悬浮态下的分解过程主要受化学反应控制,建立基于缩核模型的气固反应模型进行数值模拟,模型中的主要反应。
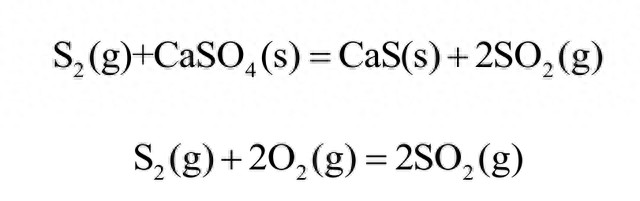
由于反应机理为化学反应控制,其边界扩散阻力和内扩散阻力可忽略不计,故可简化。
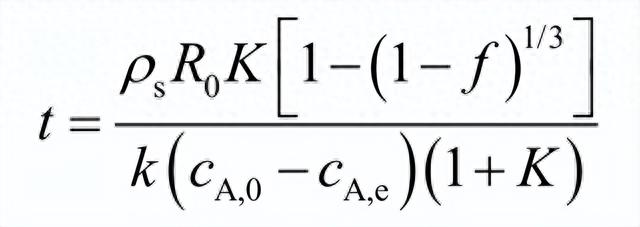
由Arrhenius方程计算得。
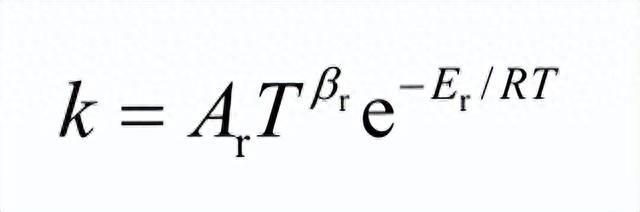
气体硫磺还原磷石膏的一步反应机理为化学反应控制,其动力学方程。

化学反应动力学方程。

在Fluent中将固相颗粒的粒径以及气固反应的速率常数导入到组分运输模型中,能够准确描述该由化学反应控制的气固反应过程。
根据ΔrGm是否小于0,判断反应进行的方向、方式和优先级次。
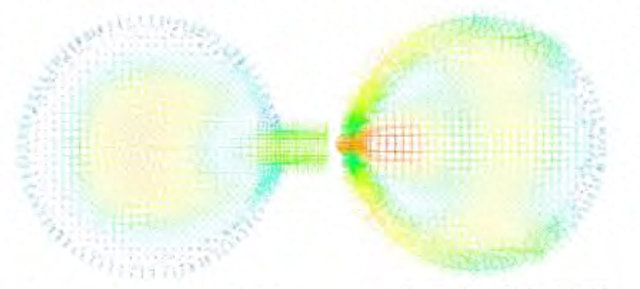
气体硫磺和磷石膏的反应温度在1073K左右才能自发进行,而磷石膏直接热分解反应温度在1573K,故无法直接分解。
在该反应阶段气体硫磺还原CaSO4生成CaS为主反应,相比于用焦炭还原磷石膏过程中的多种副反应的发生,气体硫磺预分解CaSO4阶段的温度控制较容易一些,试验煅烧温度可选择在1023~1223K。
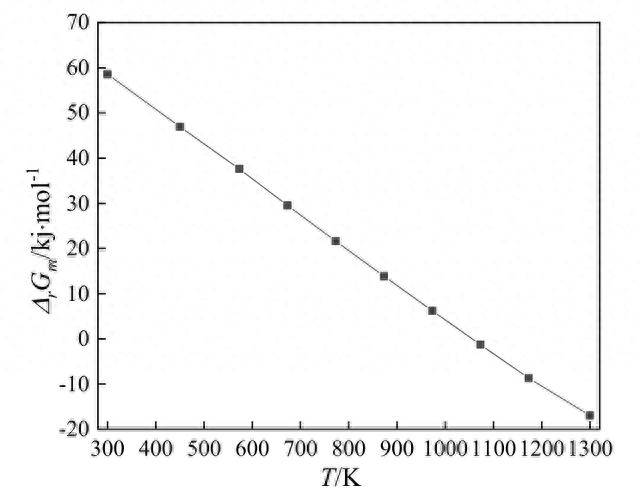
在常温下,硫单质主要以S8形式存在,随着温度升高S8会转化为S6、S4、S2等,当温度为1023K时气体硫磺体系中S2的体积分数达到97%左右。
而在还原炉中S2与CaSO4直接反应,故控制气体硫磺入口的温度应不低于1023K。
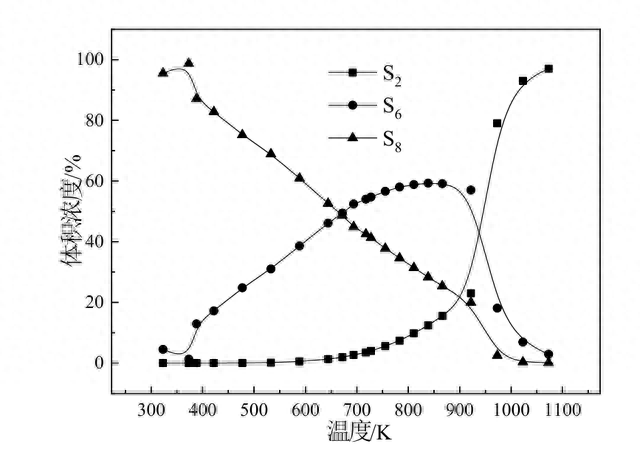
窑尾烟气入口为速度入口,出口为自由流动且离散相条件为“trap”,即颗粒运动到该边界界面时停止对其跟踪,生料颗粒和气体硫磺入口为质量流量速率,壁面为固定无滑移壁面。
窑尾烟气入口气体主要成分为O2、CO2、N2,其中O2含量控制在2%,CO2含量16%,其余均为N2,生料颗粒粒径服从Rosin-Rammler分布,最小粒径为10μm,最大粒径为80μm,中位粒径为25μm。
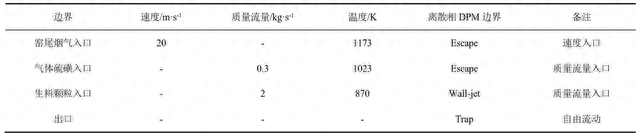
选择稳态下的压力基求解器,压力-速度耦合方式采用SIMPLEC算法,湍流动能等其他变量空间离散化选择精度更高的二阶迎风差分格式,保证设置参数满足大多数工程问题计算精度要求。
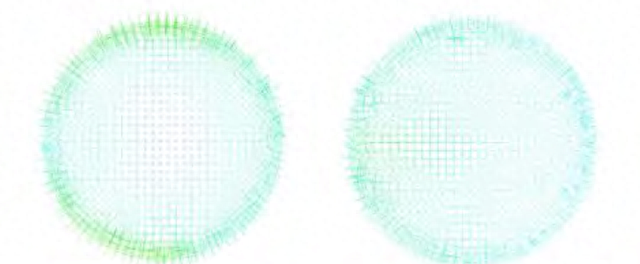
采用四面体-六面体混合网格进行模型的网格划分,为了排除网格数量对计算结果准确性的影响,选择60018、79441、117732、370557、487569、675006、909950的网格数量分别进行计算。
计算结果显示网格数量在大于30万个时还原炉内X=0截面平均温度计算稳定,考虑到计算真实性和计算资源时间,采用487569的网格数量进行后续的数值仿真计算。
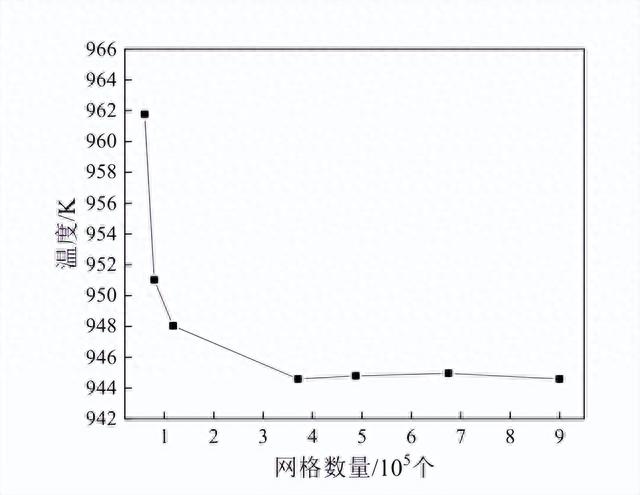
●—≺结果与讨论≻—●
两个连续相与一个离散相分别为窑尾烟气、气体硫磺和生料颗粒,三者相互作用在还原炉中形成独特的流动方式。
窑尾烟气经还原炉底部缩口进入还原炉后,速度突增,并在靠近壁面边界处形成小范围回流漩涡,随着窑尾烟气向上运动,与右侧径向进入的气体硫磺交汇形成一次喷腾效应。
继续向上运动与壁面呈60°入射的生料颗粒在Z=2.2m处交汇,使得混合流体轨迹略微发生偏移,同时伴随着混合流的速度有下降的趋势。
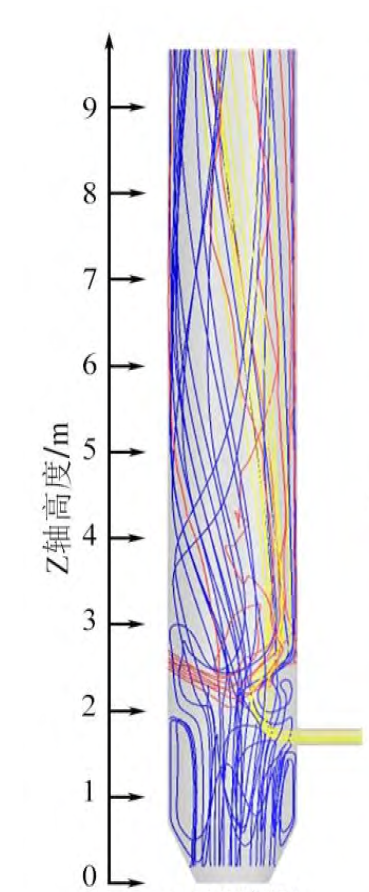
在还原炉中流动主要分为三部分,窑尾烟气经还原炉底部缩口速度突增,向上运动时速度缓慢下降的同时在还原炉下端壁面边界形成回流漩涡,与气体硫磺交汇形成一次喷腾效应。
混合气流再继续上升后与生料流接触,改变运动轨迹的同时速度随之降低,在生料入射上端由于运动轨迹被改变,导致混合流向靠近壁面边界处运动。
继续向上运动在还原炉上端形成螺旋上升的稳定流场。

在Z=1.7m处气体硫磺入射后还原炉内S2含量突增,随后在Z=1.7~4m区域范围内与进入还原炉内的生料颗粒CaSO4发生一步还原反应,同时在Z=2m区域内产生足量的SO2气体,该区域为还原炉下端的快速反应区。
在该区域内气体硫磺和O2消耗殆尽的同时伴随着SO2和N2含量的增加,系统内SO2含量的增加既能有效增加窑气中SO2的含量,使得生产工艺对原料质量要求放宽,又对后续硫酸生产SO2转化、吸收,系统生产能力提高极为有利。
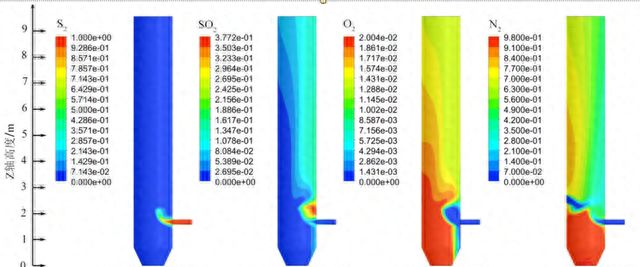
生料颗粒进入还原炉后在惯性作用下继续沿初始方向运动一段距离,随后在还原炉入口烟气和气体硫磺汇合形成的高速气流的携带作用下螺旋上升,悬浮分布于整个炉体。
螺旋上升的运动方式能延长颗粒的运动轨迹,即能有效提高颗粒在还原炉内停留时间,又能提高生料颗粒和气体硫磺的反应率,X=0截面上CaSO4、CaS的分布情况。

可以直接反映出还原炉内部CaSO4在气体硫磺的还原作用下发生的第一步反应即生成CaS的情况,在Z=2.6m附近区域内,生料颗粒从一侧入射导致其含量突增,还原炉内CaSO4含量出现极值点。
在Z=2.2~4m的快速反应区内CaSO4含量逐渐减少,主要是由于在该区域内,部分CaSO4颗粒与自下而上的气体硫磺碰撞,从而产生CaS和SO2,还原炉中大部分区域内的CaS含量较为稳定,且含量呈现整体上升趋势。
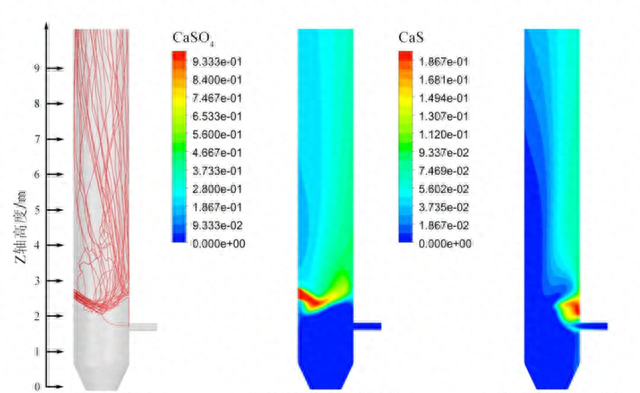
CaS作为CaSO4生料颗粒还原的产物,其含量的增加趋势是稍滞后于CaSO4的减少趋势的,观察整个炉体空间中CaSO4和CaS分布情况可知,气体硫磺还原磷石膏反应主要发生在CaSO4颗粒入射到还原炉内的上方区域和其与气体硫磺的交汇处。
在该位置控制还原炉内化学反应过程极为关键,在还原炉中部由于混合烟气与生料颗粒碰撞作用致使其运动方向发生偏移,导致在该区域混合组分轨迹偏向右侧内壁,随着反应的进行,物料随气流继续向上运动,流动形态逐渐变为平推流。
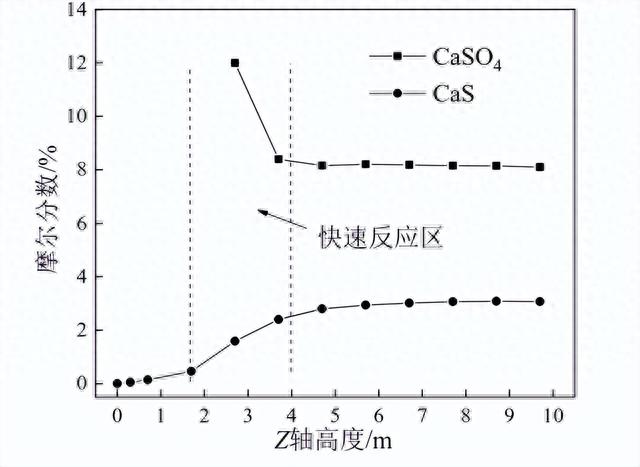
Z轴各个截面温度分布,发生化学反应的位置都伴随着温度的变化,Z=0~0.5m附近区域的温度出现一个极大值点,温度由1073K升高到1200K左右,是因为在该区域内小部分气体硫磺进入还原炉后在壁面边界处与窑尾烟气中的O2燃烧并放热。
主要作用是在小部分气体硫磺燃烧的作用下形成高温环境,使进入还原炉的气体硫磺全部转变为双原子硫,Z=1.0~3.5m区域内温度逐渐降低。

主要是由于温度870K左右的生料颗粒从壁面入射到还原炉内,伴随着还原炉内气体硫磺和CaSO4颗粒的化学反应吸收热量,导致炉内温度逐步下降。
在生料颗粒入射区域形成低温区,且在右侧壁面边界生成CaS处形成局部低温区,在还原炉中上部生料颗粒螺旋流动区域温度较低,轴心区域在混合烟气流动作用下温度较高且趋于稳定。
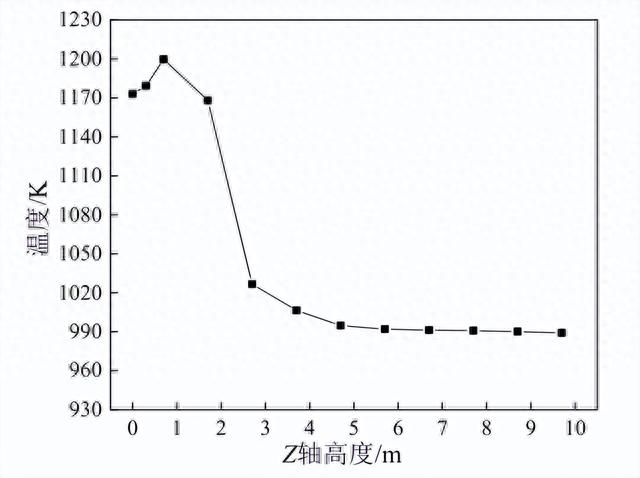
多组模拟试验结果分析得到不同n(CaSO4)/n(S2)条件下硫酸钙的分解率,同时使用Design-Expert软件对单因素影响进行分析,控制CaSO4分解率在20%~25%的范围内。
对n(CaSO4)/n(S2)的取值在2.5~3.7的范围内进行合理预测,CaSO4的分解率与n(CaSO4)/n(S2)基本上成反比例关系,该反应机理为化学反应控制。
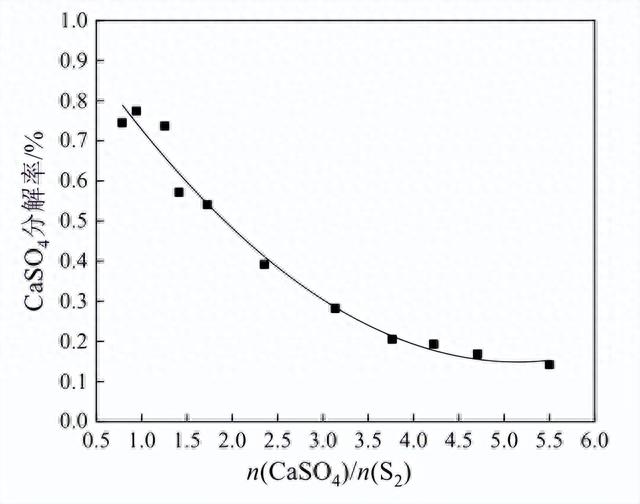
随着n(CaSO4)/n(S2)的增加,反应体系中的CaSO4摩尔分数不断增加通过反应消耗的S2量也不断增加,导致反应体系中S2摩尔分数不断减少直至消耗殆尽,反应速率逐渐降低。
硫酸钙分解率要控制硫酸钙的分解率在20%~25%的范围内,才能保证出炉物料满足深度还原的要求,故应该控制入炉n(CaSO4)/n(S2)的波动范围在3.0~3.5以内。

●—≺结语≻—●
采用CFD方法对气体硫磺还原磷石膏制酸中试装置还原炉进行了数值模拟研究,分析了还原炉内湍流和化学反应的耦合过程的温度场、组分场,得到了还原炉内气体硫磺和生料颗粒的具体物理化学变化过程。
数值仿真计算得到,在原料n(CaSO4):n(S2)为3.14:1工况下,出口生料分解率为26.84%,还原料中n(CaSO4):n(CaS)为2.72:1,满足还原要求,与实际情况相符。
还原炉内流场、组分场和温度场分布较为合理,各组分流线符合实际规律,还原炉下端反应区气固相换热充分,反应合理,上端平推区流动状态和温度都较为稳定。
参考文献:
[1]陆金驰,李东南,陈凯,等.煅烧磷石膏对蒸压硅酸盐制品水化过程的影响[J].化工学报,2012
[2]李凤玲.磷石膏分解特性与其分段煅烧制备硫铝酸盐水泥研究[D].重庆:重庆大学,2016
[3]孟令佳,吉忠海,陈津.工业副产石膏热分解脱硫的研究进展[J].化工进展,2017
[4]钟本和,王辛龙,张志业,等.硫磺还原分解磷石膏制硫酸节能减排新工艺[J].化肥工业,2014
[5]王辛龙,张志业,杨守明,等.硫磺分解磷石膏制硫酸技术进展及推广应用[J].硫酸工业,2018
[6]张国兴,陈延信,庞仁杰,等.一种硫磺气体还原石膏制硫铝酸盐水泥联产硫酸的方法:CN111559879B[P].2022